The 5s in the workplace are Sort, Set in Order, Shine, Standardise and Sustain.
Sort: Sort materials and objects into appropriate categories or areas.
Set: Establish standards, layout and expectations.
Shine: Maintain work areas and equipment in a clean and presentable condition.
Standardise: Use common work procedures and standards to improve efficiency.
Sustain: Keep the work area clean and organised.
What is the purpose of having a 5s system in the workplace?
The 5S system is a Japanese management system and a way to improve the workplace environment and productivity. The system is designed to help companies organise and streamline their work spaces. By implementing the 5S system, companies can minimise waste, increase efficiency, and improve safety.
How to implement 5s in the workplace?
To implement 5S in your workplace, you will need to determine which areas need improvement and then work to implement the steps in the correct order.
To start, it is important to identify which areas need attention. Once you have identified which areas need attention, you will need to Sort your materials and objects. This will help you to clean and organise the area. Next, you will need to Set in Order your work area. This will help you to keep your work area organised and clean. Then, you will need to Shine your materials and objects. This will help them to look their best and make them easier to use. Finally, you will need to Standardise your work area so that all materials and objects are the same way. This will help to create a uniform look and feel in the workplace.
What are 5s red tags?
5S red tags are used in the sort process at the start of the 5s implementation. They are placed on an object to indicate that it needs attention and may not have a home, is broken or not useful any longer.
5s in different work environments: blue vs white collar
The five S’s, or “Sort, Set in Order, Shine, Standardise and Sustain” can be used in a variety of work environments, from blue-collar to white-collar. In blue-collar workplaces, the emphasis is on speed and efficiency; in white-collar workplaces, the emphasis is often placed on quality and appearance.
In both types of workplaces, however, it is important to keep work areas clean and orderly, and to ensure that materials are easily accessible and usable.
5s in the workplace can help to create a more organised and clean environment. By following the 5s steps in the correct order, you can help to improve your workplace safety as well.
Reach out to CI Teams and we can assist you in training on 5S or building a 5S implementation program.
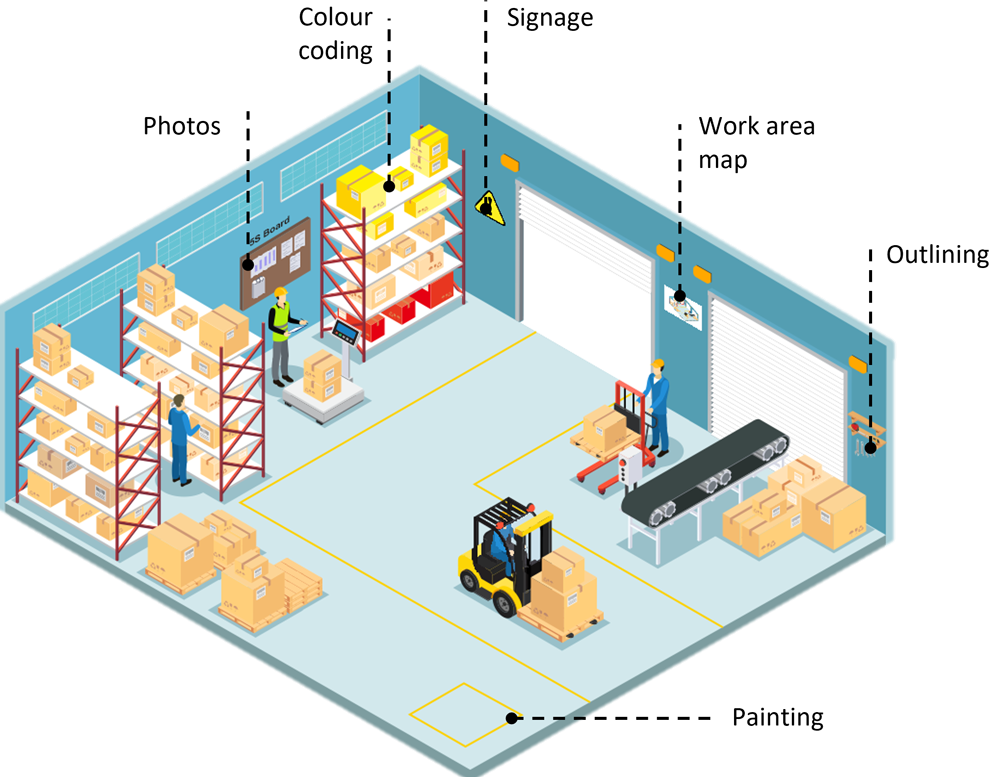